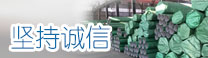
行業動態
聯系方式
聯系人: 劉經理
手 機 :136 7673 1206
電 話 : 0577-28909778
E-mail : myzhide@126.com
110KSi-40Cr厚壁無縫鋼管熱處理工藝研究
研究了110KSi-40Cr厚壁無縫鋼管調質態的顯微組織和力學性能,分析了力學性能不穩定產生的原因,隨后優化生產工藝。結果表明:40Cr鋼管性能不穩定主要原因是鋼管壁厚較厚,淬火冷卻能力不足,導致材質未淬透;從鋼管外壁往中心位置的組織演變是網狀鐵素體含量逐漸增多,回火索氏體含量逐漸減少,導致鋼管中心位置性能不合格。
40Cr是國標GB/T 3077—2015中的牌號,是一種C-Cr-Mn為主要強化元素的合金結構鋼,材料的淬透性良好,常用于制造軸類、轉向節和重要的螺栓等受力的機械零件,要求具有高的強度,良好的塑性和韌性,優異的沖擊吸收能量。常規的淬火工藝是870~890℃保溫后油冷或者淬火液冷卻。通過改善淬火工藝來提高其強韌性,成為提高40Cr鋼使用性能的有效手段。
本文研究的40Cr厚壁無縫鋼管用于汽車半軸套管,傳統生產工藝流程是:熱軋管→下料分段→粗加工→調質處理→精加工。為減少生產工序,提高生產效率,研究熱軋管直接整管調質處理,來達到相應的性能要求。40Cr鋼管設計標準性能要求為:抗拉強度≥950MPa,屈服強度≥800MPa,伸長率≥13%,20℃下的U型缺口縱向沖擊吸收能量≥65J,端面硬度要求27~33HRC。試驗用水作為淬火冷卻介質,初始工藝采用外淋內噴淬火方式,調質后性能無法達到技術協議要求,表現為性能波動較大,不同位置性能不一致。為研究性能不穩定的原因,分析了調質態的顯微組織和力學性能,隨后優化生產工藝,改為浸入內噴方式并優化淬火參數,研究相關性能指標。
1研究材料與方法
1.1研究材料
通過電爐+爐外精煉+真空脫氣工藝冶煉出40Cr鋼原料,將原料在高溫下經過壓縮比大于4.0的塑性變形軋制,軋制圓鋼公稱直徑是150mm。圓鋼在環形爐中加熱到1240~1270℃,通過太原重工生產的二輥斜軋穿孔機熱穿出空心毛管,再經過二輥精密軋管機的二次變形和熱定徑機精整成形生產出規格為φ115mm×27mm的無縫鋼管,鋼管長度5.8~6.2m。試驗40Cr鋼的化學成分見表1。
1.2研究方法
用水作為淬火冷卻介質,淬火方式首先采用外淋內噴方式,經過調質處理后,分析性能和組織,然后根據分析結果,提出改進措施,淬火方式改為浸入內噴方式并優化淬火參數,再次分析性能和組織;瘜W成分試樣按照GB/T 20066—2006加工,按照標準GB/T 4336—2006火花源原子發射光譜分析常規法檢測。微觀組織顯示劑為4%的硝酸酒精,微觀組織觀測時用德國蔡司Axio ImagerA2m金相顯微鏡。性能檢測取樣位置在鋼管壁厚的1/2處,依據GB/T 228.1—2010對試樣進行縱向拉伸性能檢測,拉伸試樣的標距為50.0mm,試樣直徑為10.0mm,檢測設備型號是SHT5605 60t。沖擊吸收能量試樣一組3個,尺寸為55mm×10mm×10mm,沿著鋼管軸線方向制樣,依據GB/T 229—2007對試樣進行20℃沖擊吸收能量檢測,取值為平均值,檢測設備型號是NI300F。硬度試樣取自鋼管橫截面,依據GB/T 230標準對試樣進行洛氏硬度檢測,三個點取平均值,檢測設備型號是TH320。
2試驗結果和分析
2.1外淋內噴方式淬火工藝對性能的影響
調質處理是一種通過獲得馬氏體相變對金屬材料加工的熱處理方式,通過加熱和冷卻實現材質微觀組織的變化,達到提高產品的性能。40Cr淬火加熱的目的是為了獲得細小而均勻的奧氏體,以便淬火后獲得細小均勻的馬氏體。淬火加熱溫度為Ac3以上30~60℃,溫度太高晶粒容易長大,淬火馬氏體容易組織粗大,沖擊韌度降低,而溫度太低組織轉變不完全,導致強度低,失去了淬火的意義[4]。本試驗40Cr鋼管規格是φ115mm×27mm,外徑小,壁厚較厚,淬火方式首先選用外淋內噴方式,淬火冷卻介質為水,圖1是鋼管的外淋內噴水冷淬火工藝示意。
外淋內噴水冷方式淬火工藝:在淬火爐中進行加熱,890℃保溫80min。然后快速放置到淬火水池上方的旋轉托輪上,旋轉速度40r/min。鋼管一側開啟內噴水,用于冷卻內表面,內噴水壓力0.21MPa。同時,外淋水從上方垂直落下,冷卻外表面,鋼管在旋轉的過程中實現冷卻,當鋼管溫度冷卻到38℃以下時,結束淬火,進入回火爐加熱,在550℃保溫120min進行回火處理。
在調質后的鋼管不同位置上截取力學性能試樣,進行拉伸、硬度和沖擊吸收能量的檢測,結果見表2。
由表2可以看出,鋼管從外壁到中間位置的抗拉強度都滿足技術指標,但波動較大,中間位置的抗拉強度比靠近外壁處低了21MPa,降低幅度約2.11%。中間位置的屈服強度不合格,比外壁處低了18MPa,降低幅度約2.11%?拷獗谔幍臎_擊性能合格,而中間位置的沖擊吸收能量比外壁處低了6J,不合格?拷獗谟捕嚷愿哂谥虚g位置的硬度。鋼管從外壁到中間位置的力學性能波動較大,靠近外壁綜合性能整體優于中間位置的性能,這是因為鋼管內孔小,且壁厚較厚,淬火過程中靠近外壁冷速快,形成的馬氏體致密細小,而中間位置壁厚的熱量要通過內外壁散熱,冷速慢,形成的馬氏體就粗大。
2.2外淋內噴方式淬火工藝對微觀組織的影響
為進一步分析鋼管性能不穩定的原因,在外淋內噴方式淬火調質后的鋼管上進行取樣,分析觀察微觀組織,腐蝕介質是4%的硝酸酒精,腐蝕時間4~8s。圖2是鋼管外淋內噴淬火方式調質后的微觀組織。
由圖2a可以看出,靠近外壁區域從奧氏體析出了少量白色條狀鐵素體和羽毛狀貝氏體,其余是細小的回火索氏體。由圖2b可以看出,壁厚的中間位置組織較差,白色的鐵素體數量增多,連接成網狀,并局部析出塊狀鐵素體,其余是回火索氏體。從材料外表面到心部組織鐵素體含量增加的現象是典型的淬火組織缺陷,符合未淬透組織特征。根據鋼的等溫轉變圖,要獲得馬氏體組織,關鍵是要在過冷奧氏體最不穩定的等溫轉變圖鼻尖溫度附近實現快冷,使奧氏體不發生鐵素體或貝氏體轉變。本試驗研究的40Cr材質,外淋內噴淬火水冷工藝,鋼的冷卻速度達不到獲得細小均勻馬氏體的要求,冷卻速度低,淬火組織中析出了鐵素體、貝氏體等有害相,回火后保留下來,導致性能不合格。
2.3浸入內噴方式淬火工藝對性能的影響
通過以上分析,對于厚壁材料,本身淬透能力減小和外淋內噴淬火方式散熱慢,導致淬火時難以達到奧氏體向馬氏體轉變要求的冷卻速度,淬火后不能獲得完全馬氏體組織,是導致性能不合格的主要原因。針對此問題提出改進措施:①在原成分基礎上,提高w Mo達到0.12%。②淬火冷卻方式改用浸入內噴式。③提高淬火拖輪旋轉速度到55r/min。④內噴水壓力提高到0.41MPa。⑤鋼管淬火時浸入水面以下200~300mm。淬火后溫度仍控制在38℃以下,在550℃保溫120min回火,圖3是鋼管的內噴浸入淬火工藝過程示意。
由圖3可以看出,采用新的淬火工藝后,外表面冷卻水流量增加,鋼管與冷卻水的接觸面積更大,表面形成的蒸氣泡膜被迅速打破,內噴水的流速和壓力得到提高,管子轉速更快,保證了冷卻速度更快且降溫更均勻。在調質后的鋼管不同位置上截取力學性能試樣,進行拉伸,硬度和沖擊吸收能量的檢測,結果見表3。
由表3可以看出,生產工藝改進后,鋼管從外壁到中間位置的各項力學性能變得更加穩定,不同位置的數據波動較小,且都在技術協議要求的范圍內,強度、沖擊吸收能量和硬度都比外淋內噴工藝有所提高。特別是屈服強度和沖擊吸收能量提高較為明顯,中間位置的屈服強度比初始工藝提高了約115MPa,提高幅度約14.52%,中間位置的沖擊吸收能量比初始工藝提高了15J,提高幅度約25%?拷獗谟捕仁30.8HRC,中間位置硬度是30.6HRC,基本一致。這說明從外壁到中間位置性能衰減比較小,改進的生產工藝提高了材質的淬透能力,淬火時的冷卻速度大于臨界冷卻速度,保證了過冷奧氏體順利越過等溫轉變圖的“鼻尖”,整個截面獲得全馬氏體含量組織。
2.4浸入內噴方式淬火工藝對微觀組織的影響
在改進的生產工藝調質后的鋼管上進行取樣,在顯微鏡下觀察不同位置的微觀組織,圖4是用改進工藝生產的40Cr無縫鋼管的微觀組織。
從圖4中可以看出,淬火后形成的板條馬氏體數量較多,板條間距小,馬氏體組織致密,外壁到中間位置的貝氏體和網狀鐵素體消失;鼗鸷笳麄截面是均勻一致的回火索氏體,細小碳化物顆粒在鐵素體基體上彌散分布。這是因為改進的生產工藝確保了過冷奧氏體向馬氏體轉變的充分性,與力學性能檢測結果數據一致。這說明,對于厚壁材料來說,通過合金成分的優化和淬火工藝的改進,能夠提高材質的淬透能力。
3結束語
1)本研究的40Cr厚壁鋼管用初始外淋內噴淬火工藝生產后,靠近外壁位置綜合性能整體優于中間位置的性能,但是中間位置處的屈服強度和沖擊吸收能量較低,這是因為鋼管的組織未淬透,靠近外壁區域從奧氏體析出了少量白色條狀鐵素體和羽毛狀貝氏體,壁厚的中間位置組織較差,白色的鐵素體數量增多,連接成網狀。
2)通過優化成分和采用新的浸入內噴淬火工藝后,外表面冷卻水流量增加,鋼管與冷卻水的接觸面積更大,表面形成的蒸氣泡膜被迅速打破,內噴水的流速和壓力得到提高,管子轉速加快,保證了冷卻速度更快,淬火后獲得完全致密馬氏體組織,鋼種的各項力學性能合格。
文章作者:不銹鋼管|304不銹鋼無縫管|316L不銹鋼厚壁管|不銹鋼小管|大口徑不銹鋼管|小口徑厚壁鋼管-浙江至德鋼業有限公司
文章地址:http://www.feiyu123.cn/Info/View.Asp?Id=1026
版權所有 © 轉載時必須以鏈接形式注明作者和原始出處
我們需要您的支持與分享
相關新聞
- 沒有資料